World’s largest and most powerful commercial jet engine: GE9X!
- Michaël
- Jan 10, 2020
- 3 min read
Fuel costs more than 20% of today`s airlines` operating expenses and companies in the industry are trying to find any possible solution to decrease the fuel consumption of the aircrafts, since the smallest improvement results to huge gains. Decreasing fuel consumption is not essential only for monetary gains, but also very important for the environment in terms of meeting stricter carbon emission limits. Actually, there are simply two ways of decreasing fuel consumption; either with a better designed aircraft (with weight savings and superior aerodynamics) or with more powerful and fuel-efficient engines.

We have seen obvious examples of this movement in the past years, where 4-engined commercial aircrafts became obsolete such as Airbus A340, Boeing 747 and even the much newer Airbus A380. These aircrafts are either retired, stopped being produced or came to the end of their operational lives, due to high operating costs despite having huge passenger and load capacities. The era now is for more efficient aircrafts with better aerodynamics built with smart materials and equipped with sophisticated engines.
Boeing 777 was one of the pioneers of this trend combining high passenger & load capacity and long-distance capability with only 2 engines. That is why it has been powered by the GE90 jet engines specifically designed for 777s by General Electric. Among the many variations of the engine, the latest one GE90-115B rated at 115.300 lbf (513 kN) and still powering the largest models 777-200LR, 777-300ER and 777F, held the Guinness World Record by being the most powerful jet engine with a thrust of 127.900 lbf (569 kN) accomplished during the certification testing in 2002. It was also the largest commercial jet engine with 128 in (330 cm) fan diameter and first ever commercial engine having carbon-fiber composite fan blades.
As all records are meant to be broken, all these features have been surpassed by its successor GE9X specifically designed for Boeing`s next generation wide-body commercial aircraft 777X. GE9X already captured `the largest commercial jet engine` title during the production phase with a fan diameter of 134 in (340 cm), as wide as the body of a Boeing 737, when paired with the engine case. `The most powerful commercial jet engine` title came a little later; despite being rated at 105.000 lbf (467 kN) of thrust, GE9X managed to clock 134.300 lbf (597 kN) of thrust during an engineering test on November 10, 2017, at GE’s outdoor test facility in Peebles, Ohio. The Guinness world record certificate for `the most powerful commercial jet engine` has been given on July 12, 2019 in order to match the 100th anniversary of General Electric.
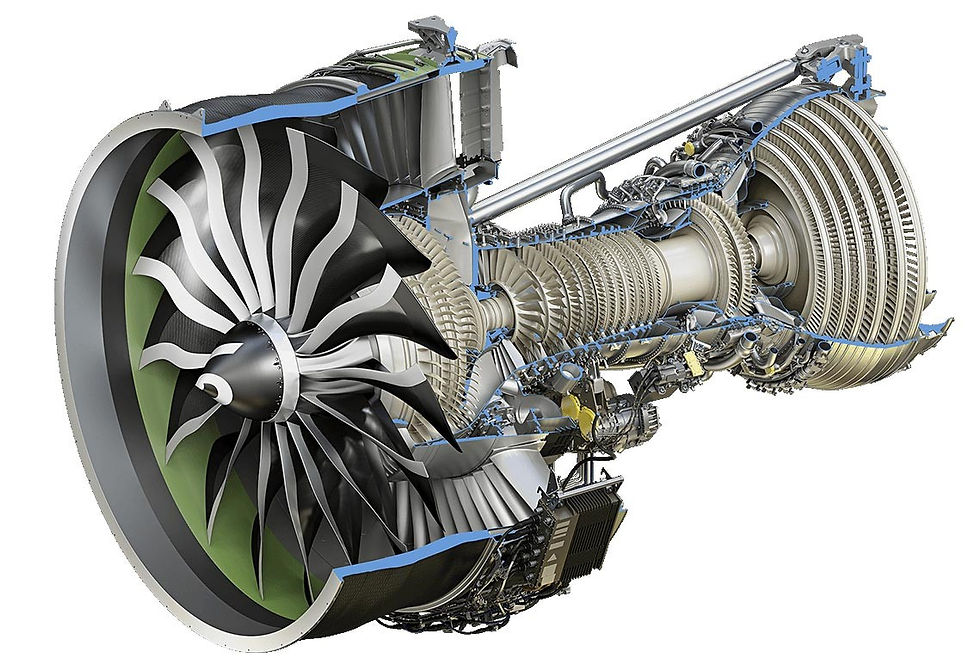
Being the largest and most powerful commercial engine are two of many attributes that GE9X engine has, since it brings many other technological breakthroughs. First of all, it can be considered as the first commercial aircraft engine to reach production with significant additive manufacturing content. The engineers could design the engine so big, because they designed fan blades and the fan case from the most advanced 4th generation carbon fiber composites, reducing the weight and cutting the number of blades from 22 to only 16, compared with its predecessor, the GE90. Of the 7 components and 304 parts being additively manufactured for the GE9X, all except the low-pressure turbine blades and the heat exchanger are cobalt chromium (CoCr) alloy parts. Stage 5 and 6 LPT blades are 3D printed from titanium aluminide (TiAl) and the heat exchanger from F357 Aluminum. The GE9X also includes 3D printed fuel nozzles produced by the GE Additive division, parts made from light- and heat-resistant ceramic composites. Similarly, the combustor and high-pressure turbine includes ceramic matrix composite (CMC) materials for twice the strength, a third of the weight and greater thermal capabilities than metal counterparts.
Thanks to these smart materials and new designs, GE9X is the most fuel-efficient engine of General Electric on a per-pound-of thrust basis and burns 10% less fuel than its predecessor GE90-115B and 5% less fuel than any other twin-aisle engine in service. In the meantime, it achieves a 27:1 compressor pressure ratio, highest ever in commercial aviation, contributing to an overall pressure ratio of 60:1 by meeting the highest noise regulations. As a result, it is not a surprise that General Electric has already received more than 700 orders.
Comments